PROFILE
Foundation of Trust
Built on Quality
www.qualityfoundation.in
Organisation Profile
Quality foundation was incorporated in the year 2005, by dedicated and hardworking professionals determined to serve the industry for a better tomorrow. We believe the foundation of any organization is built on the trust of their customers, achieved truly through quality. Hence “FOUNDATION OF TRUST BULIT ON QUALITY” is QUALITY FOUNDATION.
Over a period of Seven years we have been given the opportunity to serve for more than 200+ customers. Every customer is equally & very important for us, and is great source of strength. We sincerely strive to achieve their trust and build sustainable relationship by providing quality services, customised solutions, meeting their requirements, needs and expectations and enhance satisfaction.
We strongly believe in continual improvement in our quality services through continuing professional development of our consultants.
A brief Profile of our Founder member, senior Consultant and trainer is as follows 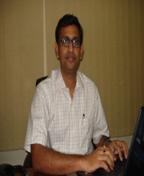
Raja Roy, Founder member of M/s Quality Foundation has the distinction of being only certified Sr. Consultant of QMS from the Eastern Region from National Board of Quality Promotion (NBQP) of Quality Council of India, India Apex body for quality promotion.
Having more than17 years of experience in diversified fields such as academics, Industry, certifications, and consultancy organizations. He has trained and consulted for more than 200+ Organizations in Various sectors, like Engineering, Manufacturing Chemicals, Petrochemicals, Pharmaceuticals, Service Industries, Automobiles, Infrastructural, Construction, Food, Hospitality, Education, IT, etc. He provides Training to various Management system Standards & Programs to Governmental Agencies, industry associations and Colleges besides industries. He is visiting faculty for TQM. He also has Research Interest on Lean Manufacturing and Supply Chain Management.
Graduated from Osmania University, University college of Technology in B.Tech (Chemical Engineering), 1994, and continued zeal to learn and deliver made him do his post graduate in Management- M.B.A. (Operations research/ Systems Management) from Jadavpur University in the Year 2002. Further his professional qualifications are:
- Certified Lead Auditor for ISO 9001- Quality Management Systems
- Certified Lead Auditor for ISO 14001- Environmental Management Systems
- Certified Lead Auditor for OHSAS 18001- Occupational Health and Safety Management Systems.
- Certified Lead Auditor for ISO 22000- Food Safety Management systems
- Certified Lead Auditor for ISO 50001- Energy Management systems.
- Certified Internal Auditor for Internal auditor for ISO/TS 16949
- Trained by Dr. Nigel Croft, ISO Technical committee member on ISO 9001:2015 - Small changes big opportunities.
- Trained at IIT kharagpur on Lean Management Tools and techniques
Benefits to the Organizations through our Consultancy & Training services
Micro Small Medium Enterprises will be benefitted by getting financial subsidy, under the Incentive Scheme of O/o Development Commissioner, Ministry of Micro Small Medium Enterprises (MSME), if they choose to get our Consultancy and Training services for ISO 9001:2015 - Quality Management system. Net Total expenses are almost Negligible.
Customised training and consultancy services which are industry specific- use of Industry specific codes, standards and practices. e.g., IT, Hospital, Education, etc.
Focus on Value addition through competent and dedicated team of consultants who have in depth knowledge on ISO standards, Possess Skills & expertise in diversified fields.
Honouring time frames and delivering on time services towards completion of the projects.
Our consultants work SAMRTly (Specific,measurable, Attainable, realistic and time bound)
Ensuring customer satisfaction and delight.
Scope of Activities
Management Systems
Consultancy Services
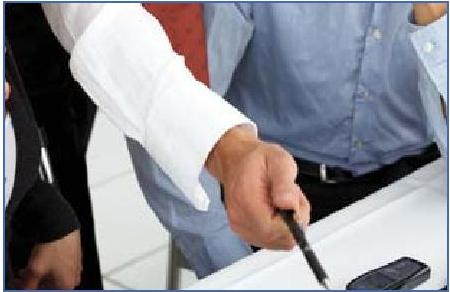 |
|
Project Consultancy & Training Services
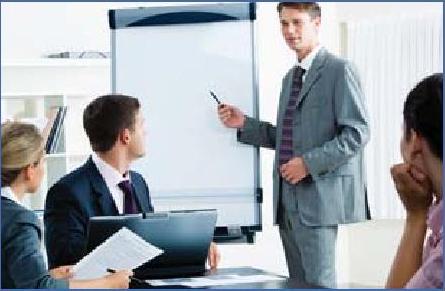 |
Project Consultancy
- Lean Manufacturing Programs
- Supply Chain Management (SCM) consultancy and training .
- Waste Management (WM).
- Development of Scientific Inventory Management (IM) and Control Systems.
- Total Productive Maintenance (TPM).
|
Training Services
Internal auditor training program on
- ISO 9001:2015 - Quality Management Systems
- ISO 14001:2015 - Environmental Management System
- OHSAS 18001:2007 – Occupational Health and safety management system
- ISO 22000:2005 – Food safety management system
- ISO 50001:2011- Energy management system.
Customised training program on further related standards on ISO 9001:2015
- ISO 9000:2005 Quality management systems – Fundamentals and vocabulary
- ISO 9001:2015 Quality management systems – Requirements
- ISO 9004:2009 Quality management systems – Managing for the sustained success of an organization -- A quality management approach
- ISO 10001:2007 Quality management – Customer satisfaction –Guidelines for codes of conduct for organizations
- ISO 10002:2004 Quality management – Customer satisfaction –Guidelines for complaints handling in organizations
- ISO 10003:2007 Quality management – Customer satisfaction – Guidelines for dispute resolution external to the organization
- ISO/TS 10004:2010 - Quality management – Customer satisfaction
– Guidelines for monitoring and measuring,
- ISO 10005:2005 Quality management – Guidelines for quality plans
- ISO 10006:2003 Quality management – Guidelines for quality management in projects
- ISO 10007:2003 Quality management – Guidelines for configuration management
- ISO 10012:2003 Measurement management systems – Requirements for measurement processes and measuring equipment
- ISO/TR 10013:2001 Guidelines for quality management system documentation
- ISO 10014:2006 Quality management – Guidelines for realizing financial and economic benefits
|
|
|
- ISO 10015:1999 Quality management – Guidelines for training
- ISO/TR 10017:2003 Guidance on statistical techniques for ISO 9001:2015
- ISO 10019:2005 Guidelines for the selection of quality management system consultants and use of their services
- ISO/TS 16949:2009 Quality management systems – Particular requirements for the application of ISO 9001:2015 for automotive production and relevant service part organizations
- ISO/TS 13485:2003 Quality management systems – Particular requirements for the application of ISO 9001:2015 for medical devices organization
- ISO 19011:2002 Guidelines for quality and/or environmental management systems auditing
Customised Training program on ISO 14001:2015 / ISO 18001:2007
- Initial Environmental Review / Gap Analysis for the organization - Duration 1 to 2 days
- Legal Compliance training – Duration – 1 day
- Aspect-Impacts Identification & Methodology for assessing significant Impacts - Duration 1 day.
- Occupational health and safety trainings
- Fire safety trainings
Customised Training program on ISO 22000:2005 / PAS/ FSSC
- Training on Food safety acts, PFA regulations & Alignment of Food safety Objectives
- Training on Good Manufacturing Practices and Good hygiene Practices
- Training on ISO/TS 22002- Prerequisite programmes (PRP) on food safety
- Industry based Hazard identification, CCP, PRP, – (Eg. Presentation attached for Bakery industry )
- Many more Training programs as per customer requirements
Customized Trainings on
- SA- 8000, NABL, GMP, Lean Manufacturing, TPM, 5S, Kaizen, SCM, IM, HR & Motivational Trainings etc
|
Management System Implementation Process Flow
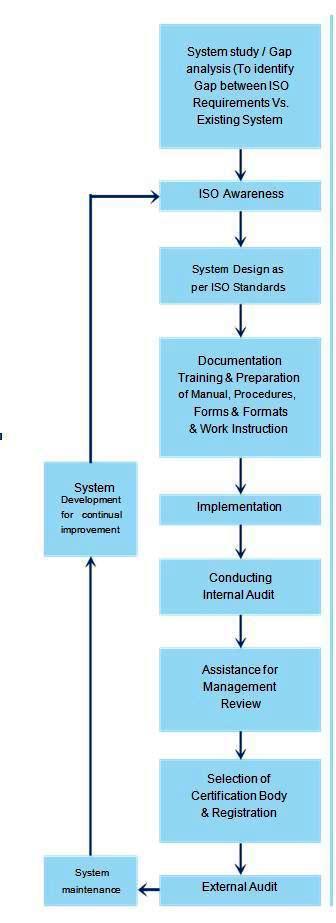 |
For a successful implementation of Management systems like Quality, Environment, Occupational Health and safety, Food Safety, Social Accountability, etc the following 7 steps are recommended. - Fully engage top management to: Define why you want to implement ISO Standard Define your mission, vision, and values in your organization Define your organization's stakeholders: customers, suppliers, etc. Define your policy, and align organizational objectives and related product/service Qualities.
- Identify key processes and the interactions needed to meet the objectives.
- Implement and manage the system and its processes (using process management techniques)
- Build your Management System -based on the relevant ISO Standard
- Identify Standard requirements
- Map these requirements with your implemented System Standard, where applicable
- Make a gap analysis: identify where in your existing system the requirements are fulfilled, and where they are not
- Include in your Management System Standard ' processes the activities, procedures and controls needed.
- Implement the system, train company staff and verify effective operation of your processes.
- Manage your Management Systems.
- Focus on customer satisfaction
- Monitor and measure the operation of your Management System Standard
- Strive for continual improvement
- Consider implementing business excellence models in the company operations.
- If necessary, seek third party certification/registration of the QMS, EMS, OH&S, Food Safety Social Accountability, etc or alternatively, issue a selfdeclaration of conformity.
Maintaining the benefits and continual improvement
The organization must strive to satisfy your customers and to achieve continual improvement of your operations through the Management System standards.
Continual improvement is a process of increasing the effectiveness of your organization to fulfill policy and objectives that you have stablished which are updated periodically. ISO Standards requires that you plan and manage the processes necessary to continually improve your Management System |
About ISO
What is ISO?
The International Organization for Standardization (ISO) ("IOS" in English, "OIN" in French for Organization Internationale de normalization) Greek "isos", meaning "equal". Therefore, whatever the country, whatever the language, the short form of organization's name is always ISO. ISO was established in 1947 and is (currently) an association of approximately 157 members, which each represent their own country with a Central Secretariat in Geneva, Switzerland.
What is a Standard?
A standard is a rule or requirement that is determined by a consensus opinion of users and that prescribes the accepted and (theoretically) the best criteria for a product, process, test, or procedure. The general benefits of a standard are safety, quality, inter-changeability of parts or systems, and consistency across international borders. |
Management Systems Philosophy/ Approach
The Plan - Do - Check - Act (PDCA) cycle is the operating principle of ISO's management system standards.
PLAN
Establish objectives and make plans (analyze your organization's situation, establish your overall objectives and set your interim targets, and develop plans to achieve them).
DO
Implement your plans (do what you planned to).
CHECK
Measure your results (measure/monitor how far your actual achievements meet your planned objectives).
ACT
Correct and improve your plans and how you put them into practice (correct and learn from your mistakes to improve your plans in order to achieve better results next time). |
Benefits derived from Quality Management Principles
Principle 1 | CUSTOMER FOCUS
Organizations depend on their customers and therefore should
Understand current and future customer needs, should meet customer requirements and strive to exceed customer expectations.
Key Benifits
Organizations depend on their customers and therefore should
Understand current and future customer needs, should meet customer requirements and strive to exceed customer expectations.
Principle 2 | LEADERSHIP
Leaders establish unity of purpose and direction of the organization.
They should create and maintain the internal environment in which people can become fully involved in achieving the organization’s objectives.
Key Benefits
- Better communication levels throughout the organization.
- Better understand of the reasons for achieving the organizations goals and objectives.
- Evaluation f activities.
- Minimizing the possibilities for error.
Principle 3 | INVOLVEMENT OF PEOPLE
People at all levels are the essence of an organization and their full involvement enables their abilities to be used for the organizations benefit.
Key Benefits
- Helping people to be motivated, committed and involved.
- Inspiring people to continually improve on their organization’s objectives.
- Making people accountable for their own performance. Stimulating people to always aim for continual improvement.
Principle 4 | PROCESS APPROACH
People at all levels are the essence of an organization and their full involvement enables their abilities to be used for the organizations benefit.
Key Benefits
- Lower costs and shorter cycle times.
|
- Effective use of resources
- Improved, consistent and predictable results.
- Focused and prioritized opportunities for improvement.
Principle 5 | SYSTEM APPROACH TO MANAGEMENT
Identifying, understanding and managing interrelated processes as a system contributes to the organization’s effectiveness and efficiency in achieving its objectives.
Key Benefits
- Being able to focus effort on the key processes.
- Being better able to achieve desired results.
- Integration and alignment of business processes.
- Promoting confidence (to interested parties) about the organization’s effectiveness, efficiency and capability.
Principle 6 | CONTINUAL IMPROVEMENT
Continual improvement of the organization’s overall performance should be a permanent objective of the organization.
Key Benefits
- Coordination of all improvement possibilities and activities.
- Improving the organizational capability.
- Providing the flexibility to react to opportunities quickly.
Principle 7 | FACTUAL APPROACH TO DECISION MAKING
Effective decisions are based on the analysis of data and information.
Key Benefits
- Ability to review, challenge and change opinions and decisions.
Principle 8 | INVOLVEMENT OF PEOPLE
An organization and its suppliers are interdependent and a mutually beneficial relationship enhances the ability of both to create value.
Key Benefits
- Ability to react quickly to a changing market and / or customer needs and
- Expectations.
- Costs optimized.
- Possibilities for creating value for both parties.
- Resources used to their best advantage.
|
Overview of Standards
ISO 9001
ISO 9001-ISO 9000 family of standards relate to quality management systems and are designed to help organizations ensure they meet the needs of customers and other stakeholders. The standards are published by ISO, the International Organization for Standardization and available through National standards bodies. ISO 9000 deals with the fundamentals of quality management systems, including the eight management principles on which the family of standards is based. ISO 9001 deals with the requirements that organizations wishing to meet the standard have to meet. Independent confirmation that organizations meet the requirements of ISO 9001 may be obtained from third party certification bodies. Over a million organizations worldwide are independently certified making ISO 9001 one of the most widely used management tools in the world today.
ISO 14001
The ISO 14000 environmental management standards exist to help organizations (a) minimize how their operations (processes etc.) negatively affect the environment (i.e. cause adverse changes to air, water, or land); (b) comply with applicable laws, regulations, and other environmentally oriented requirements, and (c) continually improve in the above.
OHSAS 18001
Occupational health and safety is a cross-disciplinary area concerned with protecting the safety, health and welfare of people engaged in work or employment. The goal of all occupational health and safety programs is to foster a safe work environment. As a secondary effect, it may also protect co-workers, family members, employers, customers, suppliers, nearby communities, and other members of the public who are impacted by the workplace environment. It may involve interactions among many subject areas, including occupational medicine, occupational (or industrial) hygiene, public health, safety engineering, chemistry, health physics.
ISO 22000
Food safety Management System - is linked to the presence of food-borne hazards in food at the point of consumption. Since food safety hazards can occur at any stage in the food chain it is essential that adequate control be in place. Therefore, a combined effort of all parties through the food chain is required. The requirements for a food safety management system that involves the following elements: Interactive communication, System Management, Prerequisite Programs, HACCP Principles. Communication along the food chain is essential to ensure that all relevant food safety hazards are identified and adequately controlled at each step within the food chain. This implies communication between organizations both upstream and downstream in the food chain. Communication with customers and supplies about identified hazards and control measures will assist in clarifying customer and supplier requirements.
Recognition of the organization's role and position within the food chain is essential to ensure effective interactive communication throughout the chain in order to deliver safe food products to the final consumer.
ISO 27000
Most organizations have a number of information security controls. Without an ISMS however, the controls tend to be somewhat disorganized and disjointed, having been implemented often as point solutions to specific situations or simply as a matter of convention. Maturity models typically refer to this stage as "ad hoc". The security controls in operation typically address certain aspects of IT or data security, specifically, leaving non-IT information assets (such as paperwork and proprietaryknowledge) less well protected on the whole. Business continuity planning and physical security, for examples, may be managed quite independently of IT or information security while Human Resources practices may make little reference to the need to define and assign information security roles and responsibilities throughout the organization.ISO/IEC 27001 requires that management:
Systematically examine the organization's information security risks, taking account of the threats, vulnerabilities and impacts;
Design and implement a coherent and comprehensive suite of information security controls and/or other forms of risk treatment
(such as risk avoidance or risk transfer) to address those risks that are deemed unacceptable; and Adopt an overarching management process to ensure that the information security controls continue to meet the organization's information security needs on an ongoing basis. |
SA 8000
SA8000 is an auditable certification standard based on the UN Universal Declaration of Human Rights, Convention on the Rights of the Child and various International Labour Organization (ILO) conventions. SA8000 covers the following areas of accountability: Child labor: No workers under the age of 15; minimum lowered to 14 for countries operating under the ILO Convention 138 developing-country exception; remediation of any child found to be working. Forced labor: No forced labor, including prison or debt bondage labor; no lodging of deposits or identity papers by employers or outside recruiters. Health and Safety: Provide a safe and healthy work environment; take steps to prevent injuries; regular health and safety worker training; system to detect threats to health and safety; access to bathrooms and potable water. Freedom of Association and Right to Collective Bargaining: Respect the right to form and join trade unions and bargain collectively; where law prohibits these freedoms, facilitate parallel means of association and bargaining. Discrimination: No discrimination based on race, caste, origin, religion, disability, gender, sexual
orientation, union or political affiliation, or age; no sexual harassment. Discipline: No corporal punishment, mental or physical coercion or verbal abuse Working hours: Comply with the applicable law but, in any event, no more than 48 hours per week with at least one day off for every seven day period; voluntary overtime paid at a premium rate and not to exceed 12 hours per week on a regular basis; overtime may be mandatory if part of a collective bargaining agreement. Compensation: Wages paid for a standard work week must meet the legal and industry standards and be sufficient to meet the basic need of workers and their families; no disciplinary deductions. Management Systems for Human Resources: Facilities seeking to gain and maintain certification must go beyond simple compliance to integrate the standard into their management systems and practices.
ISO/IEC 17025
Laboratories use ISO/IEC 17025to implement a quality system aimed at improving their ability to consistently produce valid results. It is also the basis for accreditation from an Accreditation
Body. Since the standard is about competence, accreditation is simply formal recognition of a demonstration of that competence.
A prerequisite for a laboratory to become accredited is to have a documented quality management system. The usual contents of the quality manual follow the outline of the ISO/IEC 17025 standard
Good manufacturing practice or GMP
Good Manufacturing Practice or GMP is part of a quality system covering the manufacture and testing of active pharmaceutical ingredients, diagnostics, foods, pharmaceutical products, and medical devices. GMPs are guidelines that outline the aspects of production and testing that can impact the quality of a product.
Many countries have legislated that pharmaceutical and medical device companies must follow GMP procedures, and have created their own GMP guidelines that correspond with their legislation.
A few basic principles. are : Manufacturing processes are clearly defined and controlled. All critical processes are validated to ensure consistency and compliance with specifications. Manufacturing processes are controlled, and any changes to the process are evaluated. Changes that have an impact on the quality of the drug are validated as necessary. Instructions and procedures
are written in clear and unambiguous language. (Good Documentation Practices) Operators are trained to carry out and document procedures. Records are made, manually or by instruments, during manufacture that demonstrate that all the steps required by the defined procedures and instructions were in fact taken and that the quantity and quality of the drug was as expected. Deviations are investigated and documented. Records of manufacture (including distribution) that enable the complete history of a batch to be traced are retained in a comprehensible and accessible form.
The distribution of the drugs minimizes any risk to their quality.
A system is available for recalling any batch of drug from sale or supply. Complaints about marketed drugs are examined, the causes of quality defects are investigated, and appropriate measures are taken with respect to the defective drugs and to prevent recurrence.
Lean manufacturing or lean production
Lean Manufacturing or Lean Production often simply, “Lean,” is a production practice that considers the expenditure of resources for any goal other than the creation of value for the end customer to be wasteful, and thus a target for elimination. Working from the perspective of the customer who consumes a product or service, "value" is defined as any action or process that a customer would be willing to pay for. Basically, lean is centered on preserving value with less work. Lean manufacturing is a management philosophy derived mostly from the Toyota Production System (TPS) (hence the term Toyotism is also prevalent) and identified as "Lean" only in the 1990s.It is renowned for its focus on reduction of the original Toyota seven wastes to improve overall customer value, but there are varying perspectives on how this is best achieved. The steady growth of Toyota, from a small company to the world's largest automaker, has focused attention on how it has achieved this.
Lean manufacturing is a variation on the theme of efficiency based on optimizing flow; it is a present-day instance of the recurring theme in human history toward increasing efficiency, decreasing waste, and using empirical methods to decide what matters, rather than uncritically accepting pre-existing ideas.
|
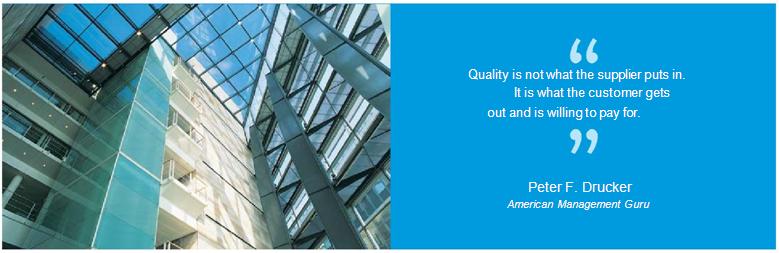 |
Few of our esteemed clients
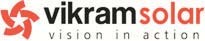 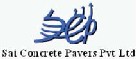 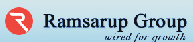  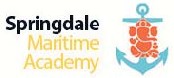 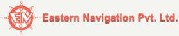    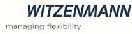 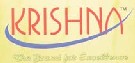 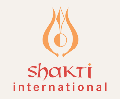 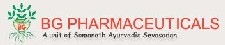 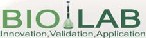  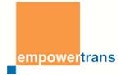    
|
|